Operational carbon linked to the running of buildings is being significantly reduced. Driven by new technologies and above all stricter regulations, new buildings have improved their energy performance and reduced their energy consumption and the associated carbon emissions for heating, cooling, lighting, and ventilation. Increasingly often “low-consumption”, they can also now sometimes state that they are “passive” or even “energy-positive”, especially thanks to an ultra-high-performance envelope and the production of their own energy.
However, reducing operational carbon alone cannot guarantee the creation of zero-carbon buildings, for one simple reason: there is also another form of carbon that has barely been taken into account to date: “embodied” carbon.
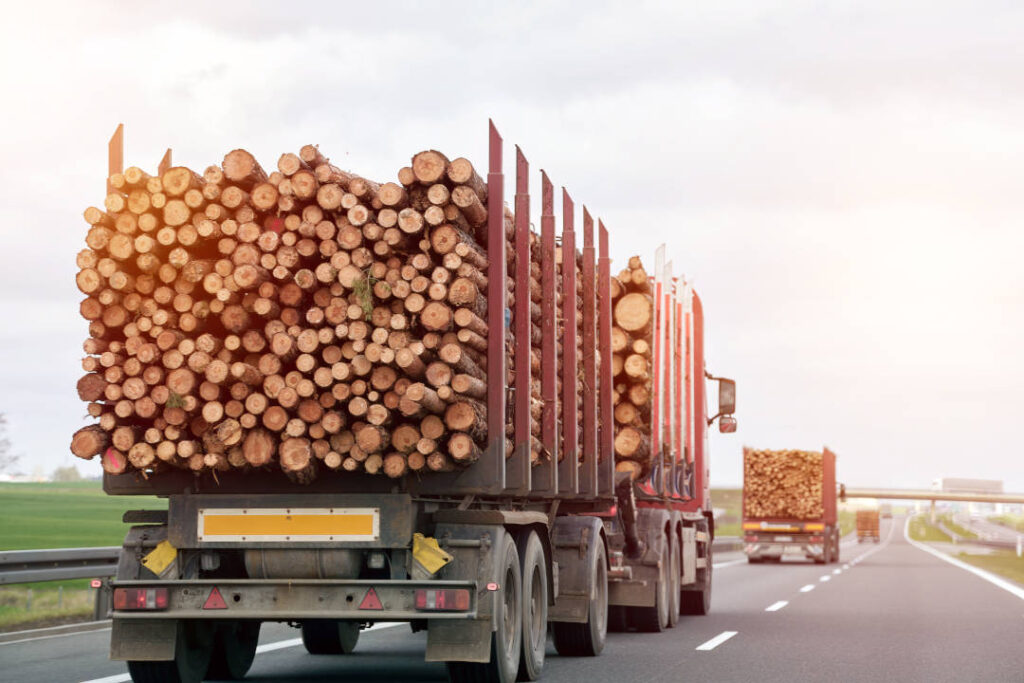
“Embodied carbon” denotes emissions associated with the manufacture and implementation of building materials throughout their life cycle, from extraction of the raw materials to their end of life. These emissions can represent up to 50% of a building’s CO2 emissions. “Embodied” carbon is linked just as much to new builds as renovations – insulating a heat-leaking structure, renovating a roof, or even simply replacing the carpet or refreshing the painting.
Unlike operational carbon, which can be addressed throughout the building’s lifetime – especially through energy retrofitting –, “embodied” carbon is emitted once and for all and no action can reduce it once the building is built or during its renovation.
Faced with the challenge of decarbonization, construction stakeholders are endeavoring to reduce their products’ carbon footprint, particularly by using carbon-free energy in their manufacturing processes and lower-carbon raw materials. It is also possible to take action in terms of building design, choosing light construction methods, for instance, or reusing products and materials.
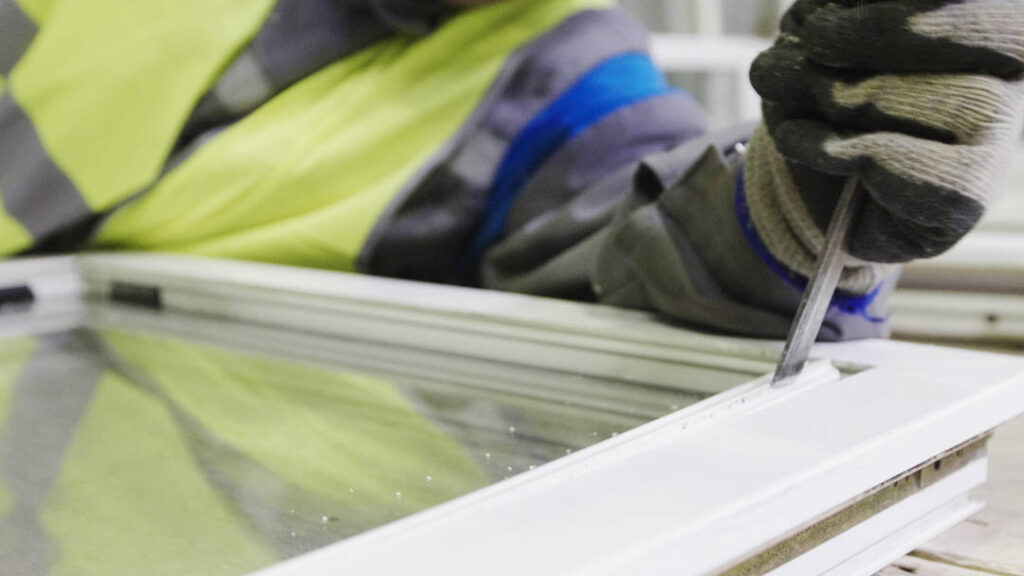
Photo credits: ©Shutterstock, © AlexGo/Adobe Stock, © Covanord