The widespread availability of generative artificial intelligence marks a decisive turning point in our relationship with digital tools. Interaction with these technologies has become considerably simpler, letting professionals exploit their potential through intuitive interfaces while drawing on their specialist expertise. This evolution, which goes far beyond simple ease of use, is deeply transforming professional construction practices. The synergy between artificial intelligence and human know-how opens up new prospects for optimizing every phase of a project, from design to operation, with a common goal: to create more sustainable and efficient buildings.
AI redefines architectural design
The emergence of artificial intelligence has revolutionized the design phase, traditionally time-consuming and iterative. Architects now have access to digital assistants capable of exploring hundreds of possible variations for a single project in just a few minutes, taking multiple parameters into account: energy performance, environmental impact, cost, comfort of occupants.
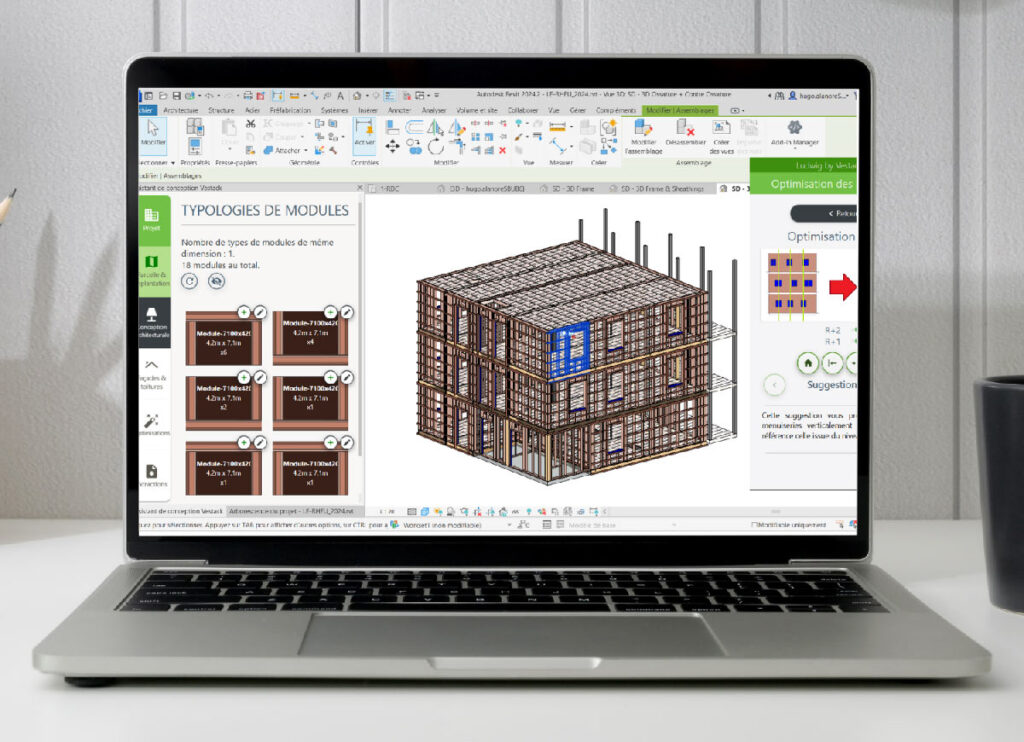
The Hypar platform is a perfect illustration of this quiet revolution. By harnessing the power of large language models (LLMs), it automates the generation of optimized plans. The first step is for users to input their requirements and constraints relating to various criteria such as energy efficiency or environmental impact. The tool then generates optimized building plans in just a few minutes. The result of automating this often time-consuming technical process is a significant improvement in productivity. This saves precious time that the design teams can use to focus more on the creative and strategic aspects of their projects.
Also, in the pursuit of optimization, Autodesk Fusion opens up the field of possibilities a little further, through the use of machine learning algorithms. The software analyzes the project constraints – solar exposure, main vents, topography – to suggest fine tuning of the building’s design and orientation. The goal is to naturally maximize thermal comfort while minimizing energy requirements.
Production: artificial intelligence for greater efficiency
AI is also revolutionizing production lines, notably through the emergence of AI-controlled robotics. Vestack offers a remarkable illustration of this with its innovative off-site construction process. The company’s smart robots are not pre-programmed; their actions are determined in real time through AI-generated algorithms. These machines analyze each component to be assembled and then automatically define their own sequence of movements, so that tasks such as high-speed nailing can be carried out precisely and as quickly as possible. Far from replacing humans, this development is redefining trades in the sector, with the emergence of new jobs such as robot operator
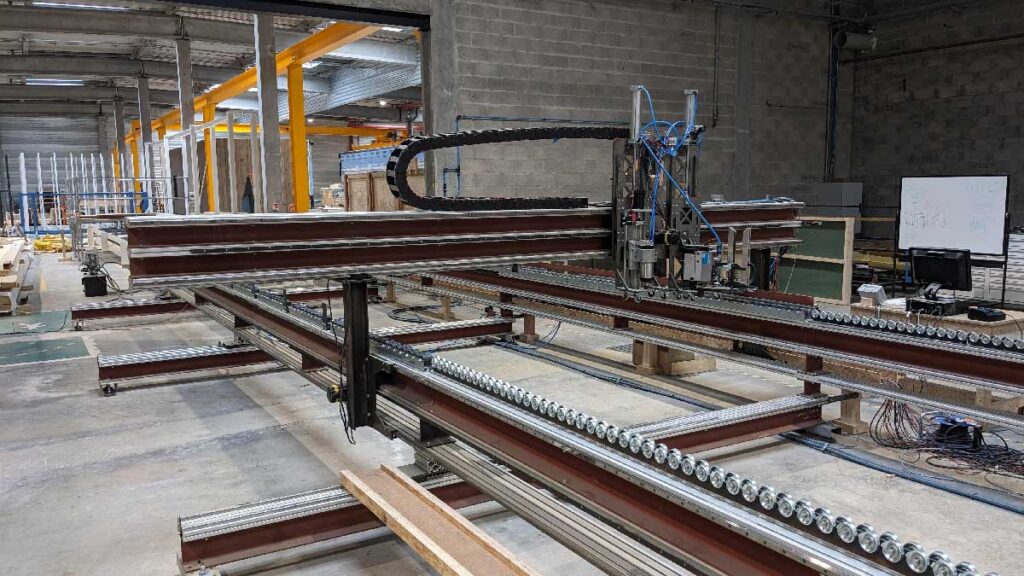
Innovation is also to be found in the formulation of materials, as demonstrated by Concrete Copilot. Using generative AI, this tool can come up with millions of possible mix formulas in just a few moments. This enables manufacturers to identify the most suitable concrete mix for a given application. A design process that used to take several weeks is now completed in a matter of minutes, while guaranteeing compliance with engineering, safety and performance standards. The results? In addition to boosting productivity and cutting costs, this approach can reduce the carbon footprint of concrete by 30%.
Through use of generative AI, the carbon footprint of concrete can be reduced by 30%. Source: Concrete Copilot
This digital transformation is also of benefit to the plasterboard manufacturing sector. Imagine algorithms that can determine panel placement with unprecedented precision, to reduce cutting and waste. This optimization even paves the way for pre-cutting in the factory based on digital mock-ups, meaning that ready-to-install “assembly kits” can be delivered to building sites. This results in considerable time savings during installation, less waste, and lower energy consumption during the construction phase. Offcuts could also be immediately returned to the production cycle, a perfect example of the circular economy.
Smart buildings: AI bringing structures to life
What if buildings could adapt to the daily routines of their occupants? We’re not quite there yet, but buildings can already use AI to analyze their pace of life. For example, by cross-referencing data linked to the number of Wi-Fi connections at certain times of the day or week, they can “deduce” that all teams are present on Tuesdays, that offices are empty on Fridays due to home working, and that some floors are busier than others depending on the time of day. This valuable data enables these new-generation buildings to adjust the ventilation, heating and air-conditioning accordingly.
This is already happening, with solutions such as Honeywell Forge. The platform deploys machine learning algorithms to control a building’s technical equipment. HVAC (Heating, Ventilation, Air Conditioning) systems are constantly adjusted to achieve two goals that were once difficult to reconcile: reducing the energy footprint while enhancing user comfort.
Innovation goes a step further with ARIA, the virtual assistant developed by BrainBox AI. This digital concierge revolutionizes day-to-day building management by combining predictive analysis and smart automation. From early detection of anomalies to energy optimization and direct dialogue with occupants via voice or text interfaces, ARIA represents the next generation of virtual technical managers.
This integrated intelligence even opens up new prospects for the end-of-life of buildings. Algorithms can now plan for optimized demolition, identifying materials that can be recovered and coordinating their re-use in future projects. This approach radically transforms traditional demolition into a methodical dismantling process and maximizes opportunities for re-use through a circular economy approach.
Artificial intelligence systems are emerging as powerful tools in the transformation of the construction sector, paving the way for more efficient, sustainable and comfortable buildings. This development marks the dawn of augmented architecture, where AI in synergy with human expertise acts as a catalyst to make sustainable construction a reality.
Photo credits: Vestack