A LIRE AUSSI : QU'EST CE QUE LA CONSTRUCTION DURABLE ?
CAALA: Instant life-cycle assessment
Developed by the German company CAALA (Computer Aided Architectural Life-Cycle Assessment), the PLCA® parametric building life-cycle assessment software provides property developers, architects and local authorities with assistance in designing carbon-neutral buildings and decarbonizing existing buildings. It takes into account energy balances, ecological analyses and life-cycle costs in real time, right from the decision-making phase.
Besides leveraging life-cycle analysis (LCA) and life-cycle costing (LCC) to develop its solutions, the software’s innovativeness lies in its speed of calculation. First, it creates a virtual twin of the building to be constructed or renovated. If appropriate, customized parameters may be added: materials, construction technologies, emission factors, costs, etc. The software then analyzes and visualizes the data, to provide an estimate of CO2 emissions, energy demand and costs, during the construction and operating phases. Ultimately, architects and developers can adjust the parameters to reach the best compromise for the final design.
Discover : a closer look at sustainable construction terms
CarbiCrete: Cement-free concrete
The Canadian company CarbiCrete has gained recognition for their patented concrete block manufacturing technology, which uses steel slag as a binder instead of cement. The first benefit of this process is to avoid the use of cement, whose energy-intensive production accounts for 8% of the world’s annual CO2 emissions (2.5 billion tons). The second involves the carbonation process, whereby the injection of carbon dioxide into fresh concrete hardens the slag and binds it together.
This innovation makes it possible to manufacture concrete blocks with up to 30% greater compressive strength: they are more resistant to the freeze/thaw cycle, and have the same water absorption capacity as conventional concrete. As a result, any plant producing precast concrete blocks (PCBs) using CarbiCrete technology clearly commits to environmental protection: each year, this process saves nearly 20,000 tons of CO2 equivalent, 33,000 tons of waste and 4,400 m3 of water.
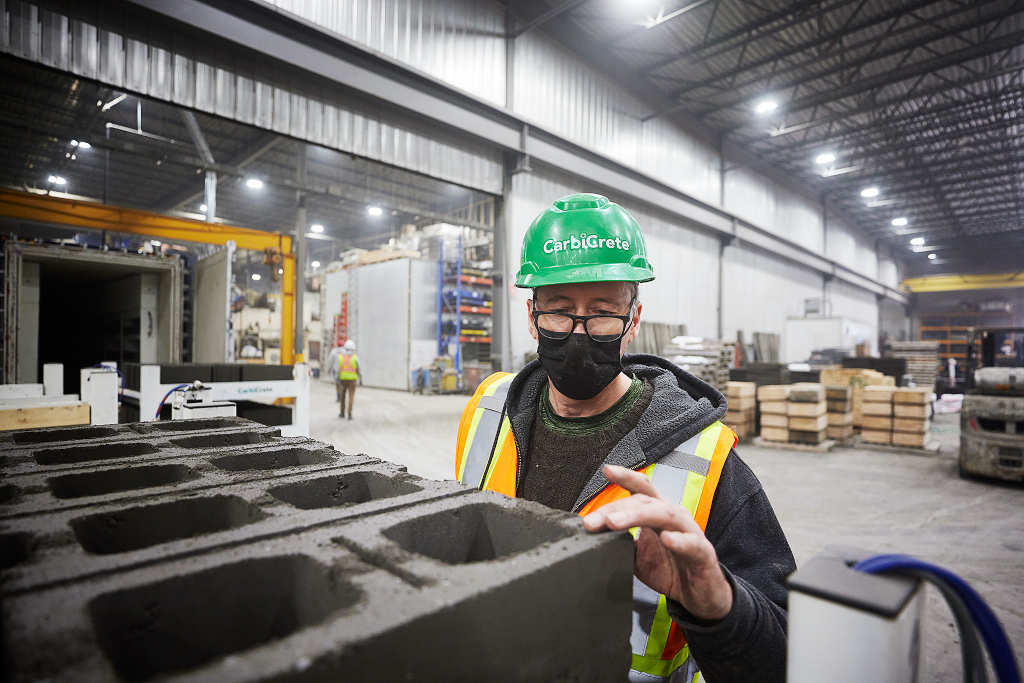
JuuNoo: The concept of reusable walls
The Belgian startup JuuNoo (winner of the Deloitte’s 2022 Technology Fast 50 in the Sustainability category) produces unique office partitions: not only do they take seven times less time to install than traditional walls, but above all, they can be reused at the end of their life. Based on the circular economy principles of “reduce, reuse, recycle”, this innovation addresses the fact that every year, around the world, over 300 billion euros worth of partitions are demolished and disposed of, with 99% ending up in landfill.
JuuNoo is particularly attentive to aesthetics and acoustics. Their patented wall partitions are made up of adaptable telescopic steel modules and recycled panels which form their aesthetic skin. They contribute to the creation of more sustainable office buildings, and offer a choice of decorative, clip-on and paintable panels. Endlessly reusable, the partitions are designed to be purchased only once. The company even buys them back from their clients if they no longer need them.
African Bamboo: Bamboo to replace aluminum
Through their pioneering materials made of natural fibers, the Dutch-Ethiopian company African Bamboo aims to create sustainable alternatives to conventional building materials, such as plastic, aluminum, steel, glass and concrete. This exclusive, smart, and low-carbon technology is more than welcome in an industry accounting for 50% of materials and raw materials production, and 40% of energy consumption and carbon emissions. Embodied carbon emitted by building materials such as steel and cement contributes to the emission of over 3,000 megatons of CO2 per year. These materials also require considerable resources and costs to manufacture, transport and install.
From cladding and furniture to flooring and load-bearing walls, African Bamboo’s products are revolutionary thanks to Yushania alpina, a non-invasive bamboo species with exceptional properties. Half as light as concrete, they are extremely robust (with a strength-to-density ratio three times higher than stainless steel) and have a life-cycle of 20 years when exposed to outdoor weathering. Moreover, their bamboo sourcing is socially, environmentally and economically sustainable. Like all six startups, African Bamboo is supported by NOVA, Saint-Gobain’s external venture entity. They work with nearly 2,200 farmers in 31 cooperatives across Ethiopia, cultivating plants manually and with as little impact as possible.
Unity Homes: Tailor-made prefabrication
Unity Homes, a home builder in the northeastern United States, implements processes designed to create sustainable, energy-efficient homes, while minimizing waste. To achieve this, the startup has developed five flexible, expandable platforms. They produce a basic construction model, which then embeds information about the site and the buyer’s preferences. Next, a 3D model of the home design is drawn up, using pre-designed elements, such as kitchens and bedrooms. Subsequently, the building’s major components are prefabricated in a computer-aided manufacturing facility. When finished, they are transported to the construction site, and assembled by a team of carpenters.
Digital technologies used by Unity Homes, help spark a resurgence in prefabricated modular homes. More cost-effective and efficient to build, they leave a much smaller ecological footprint than a traditionally built home.
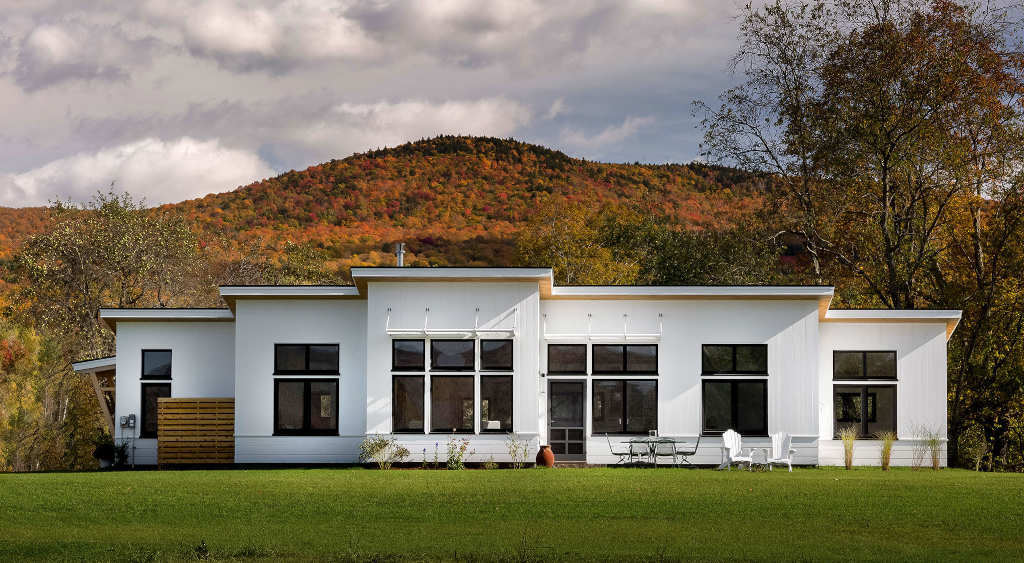
A modular home made from prefabricated beams and frames can reduce waste by 52%, and emit up to 45% less carbon than a conventional home.
Tvasta: Affordable 3D-printed housing
Tvasta Manufacturing Solutions, an Indian startup specializing in building materials, has developed a 3D concrete printing technique that can be used to build houses. This solution led to the construction of India’s first 3D-printed house in just 21 days.
Tvasta makes its system available to all players in the construction industry, whether for low-cost housing programs or large-scale infrastructures. In this context, the startup designed two buildings in 3D, for the removal and recycling of personal protective equipment for healthcare professionals, in the midst of the Covid-19 epidemic. 3D construction allows to considerably reduce waste, and ensures only the required amount of materials is used. It is also faster and safer than conventional construction.
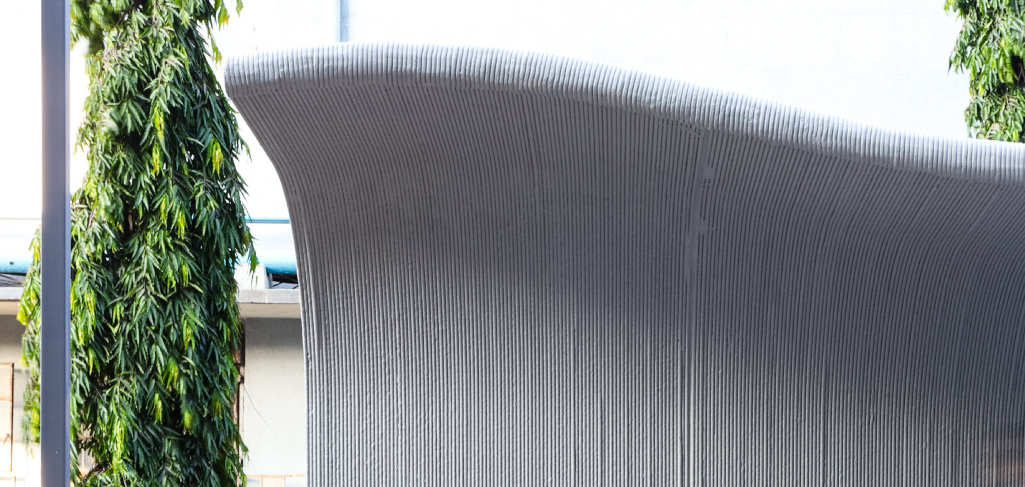
Photo credits: ©Aila Images_Stoksy, ©CarbiCrete at Patio Drummond, ©Unity Homes, ©Tvasta