Industrial insulation, i.e. the insulation of technical and mechanical plants and structures, generally concerns complex facilities consisting of numerous pipelines combined with tanks, heat exchangers, distillation columns, vessels, etc. Traditionally practiced to ensure process efficiency and preserve safety (hot or very hot process temperatures can exceed 600°C or even 1,000°C), better insulation is also a strategic choice for construction companies looking to cut energy bills and reduce CO2 emissions.
Considerable room for improvement
In a white paper published in July 2024, the European Industrial Insulation Foundation (EiiF), found that the energy efficiency of industrial plant insulation systems was poor. Almost all heat audits identify uninsulated components, such as valves, critical components on a pipeline. The EiiF states that “The savings potential exists across all regions, sectors, equipment and operating temperatures.”
This is because improving insulation can be more complex when it involves encapsulating the components concerned. Manufacturers should seize opportunities to renew equipment or carry out heavy maintenance, and take thermal efficiency into account right from the design stage of new facilities.
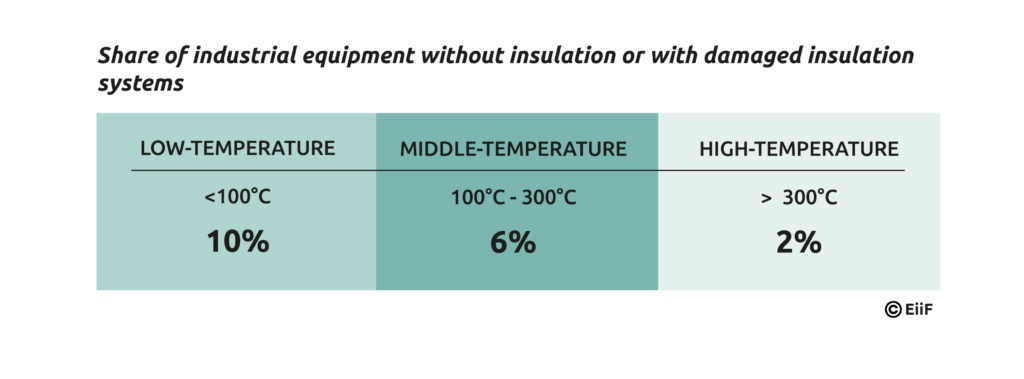
How to assess the need for industrial insulation
To assess the performance of insulation devices, the EiiF has developed the Tipcheck method, which stands for “Thermal Insulation Performance Check”. More than 3,000 Tipcheck audits have been carried out since 2010. According to the EiiF, three out of four clients invest following audits, which have already generated a cumulative saving in energy consumption of 4 TWh and a reduction in CO2 emissions of 1 Mt.
In practical terms, the surfaces concerned are identified using thermal imaging cameras and annual losses are estimated using a standardized thermal analysis tool. Pipes, valves, tanks, boilers, heat exchangers and vessels can all be insulated or better insulated.
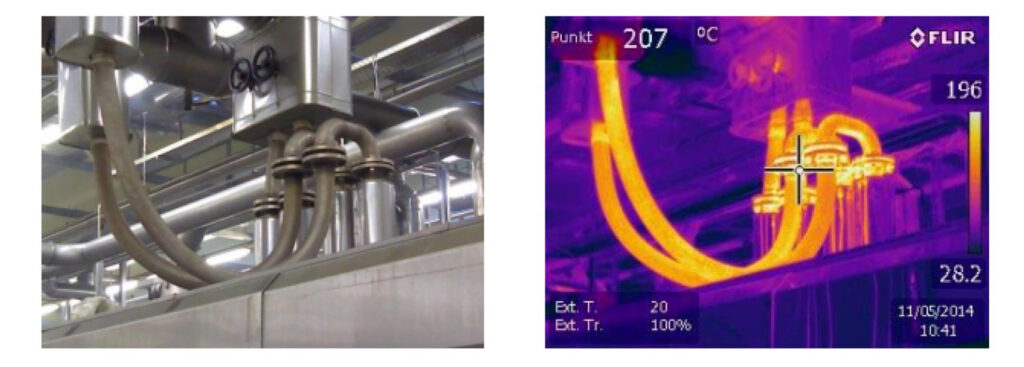
Very significant potential savings
Energy
According to the EiiF, the savings potential is huge: modernizing and optimizing industrial insulation systems would save 14 Mtoe across Europe, equivalent to 160 TWh – more than the annual energy consumption of 10 million households. This potential obviously varies from one region and sector to another, due to differences in energy use and sources, and temperature profiles. Generally speaking, upgrading insulation systems can reduce energy losses from a given source by 78% to 88%, depending on the process temperature (low, medium or high).
Carbon emissions
Insulation is also industry’s best friend when it comes to reducing its carbon footprint. Less energy is needed to maintain the required fluid temperature, leading to lower fuel consumption which translates directly into lower emissions. Well-insulated pipes also reduce the risk of leaks, further cutting energy consumption and emissions.
Improved insulation could reduce CO₂ emissions from EU industry by 40 Mt a year
Profitability
Improving the insulation of industrial facilities is also essential in terms of economic performance. Against a backdrop of rising energy costs, insulation plays a key role in reducing or eliminating heat losses, thus cutting operating costs and generating a competitive advantage in sectors where profit margins are tight.
Industrial insulation is also a way of preserving the integrity and value of industrial assets over the long term. Poor insulation can accelerate wear and tear, leading to more frequent breakdowns.In contrast, an efficient system prevents corrosion, reducing maintenance costs and deferring the need for equipment replacement.
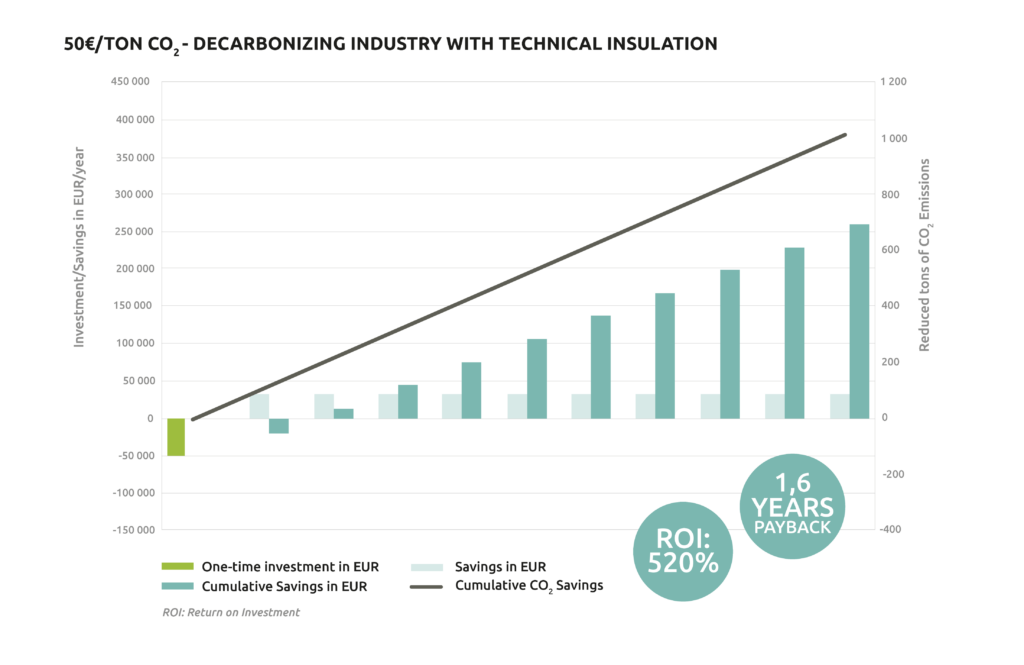
A new standard to speed up insulation upgrades by European manufacturers
Operators who have not yet done so are encouraged to upgrade their insulation. The new standard EN 17956, which came into force on December 1, 2024, encourages them to insulate all their equipment and pipes. This new standard, which takes precedence over any similar national standards, is a major milestone for industry.
This classification system is independent of the energy source and applies to new facilities (in the planning phase), those under construction and existing plants. It thus enables comparisons to be made between facilities, and provides an insulation and assessment method for each type of equipment. The European Industrial Insulation Foundation recommends aiming for at least energy efficiency rating C.
See also: Game of norms: the rules of the game in the building sector
Improving thermal insulation and energy efficiency: the example of the Xella plant in the Netherlands
The Xella plant in Landgraaf (Netherlands) specializes in building materials (sand-lime bricks, aerated concrete) and mineral insulation panels. Improving the site’s thermal insulation focused on facilities such as a large autoclave with a steam tank, a condensate tank, and the pipework (including the steam lines). The process temperatures in this equipment range from 80 to 200°C.
Given the complexity of the plant, the challenge was to optimize the thickness of the insulation, hence the use of more efficient insulation, in this case glass wool in crimped rolls. The site was thus able to reduce its energy costs and CO2 emissions, while benefiting from a tax deduction (up to 45% of the investment cost). The investment in energy efficiency techniques generated an average return of 11%.